In addition to the leadership skills and knowledge you will acquire, pursuing Lean Six Sigma certification can put you on the fast track for lucrative executive and management roles, and boost your salary. This course is part of the upcoming Lean Six Sigma Black Belt eight course bundle, designed to prepare you for the IASSC Black Belt exam.
Highlights:
- 72 practical tutorials with videos, reference guides, exercises and quizzes.
- Understand the requirements and application process for Lean Six Sigma certification with internationally recognized accreditation body, IASSC.
- Learn the roles, phases, and deliverables of a Lean Six Sigma project and your responsibilities as a Black Belt project leader.
- Master Lean Six Sigma fundamentals, including Critical to Quality (CTQ), variation, and process management.
- Become a subject matter expert in the five phases of DMAIC: Define, Measure, Analyze, Improve and Control.
- Learn techniques to coach stakeholders and provide positive and negative feedback.
- Identify the deliverables required for each Stage gate review and how to isolate issues.
- Aligned to the IASSC Lean Six Sigma Black Belt Body of Knowledge.
- Designed to prepare you in part for the IASSC Black Belt exam, alongside seven accompanying courses.
- The only method to earn an IASSC certification is to successfully sit for and pass an official IASSC certification™ exam, which can be taken through IASSC. We do not provide access to IASSC Certification exams.
- Earn 30 PDUs or contact hours toward your Project Management education for certification with PMI.
Once enrolled, our friendly support team is here to help with any course-related inquiries.
Summary
- Skill level: Advanced
- Lessons: 72
- Pre-requisites: None
- Estimated study time: 38h for all materials
- Certificate: Yes
- Accredited by: CPD
- Video duration: 7h 07m
Features
Premium video tutorials
Personalized Learning
Learn at your own pace
Tests and Quizzes
Award winning instructors
Get Certified
Mobile - Learn on the go
Regularly updated content
Accreditations & Approvals
All courses under each learning path are accredited and approved by one or more of the following bodies as is applicable.
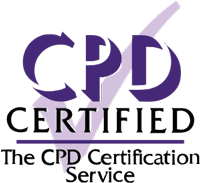
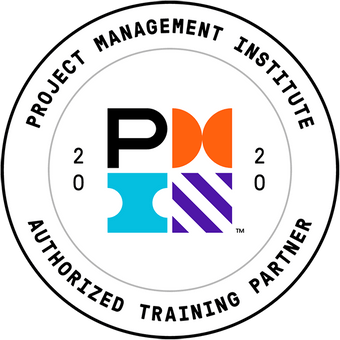
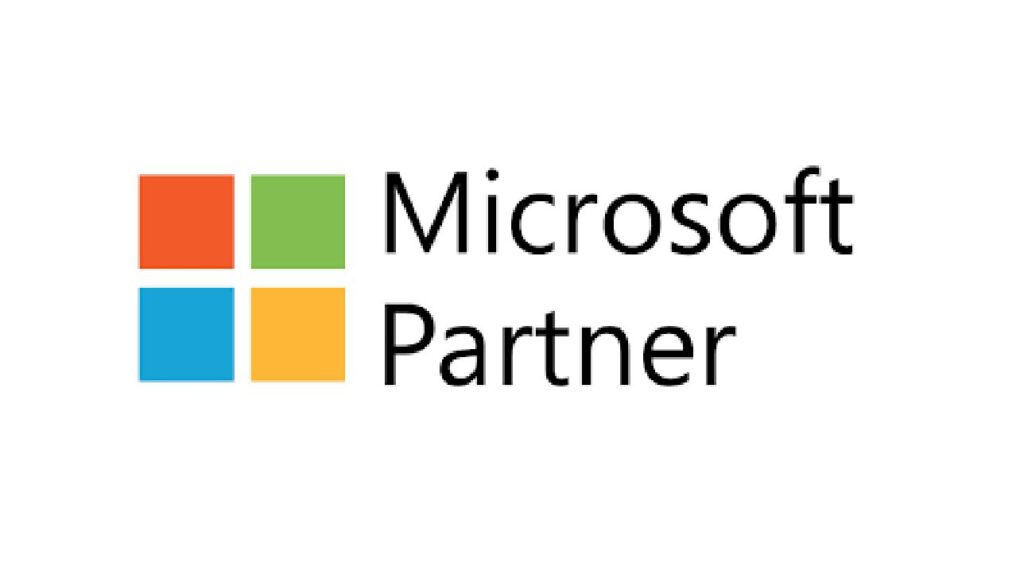
Instructors
All courses are taught by reputed trainers with relevant accreditations and industry experience.
Modules
History of Continuous Improvement
Lean Six Sigma is a proven business process improvement methodology that builds on the best practices and experiences of earlier approaches. It combines best practices around customer focus, empowered teams, process definition, and data analysis.
Six Sigma Principles
Lean Principles
Lean and Six Sigma
Lean and Six Sigma are easily blended. They have many similarities in methodology – process focused, team based, and project management. The differences, analyzing quality data versus flow data, are complementary and together provide a balanced view of the process.
IASSC Testing Approach
IASSC Black Belt
This lesson provides a high-level review of the topics covered on the IASSC Black Belt examination.
Roles and Responsibilities
Project Phases
The Lean Six Sigma methodology relies on a five-phased project management methodology. The phases Define, Measure, Analyze, Improve, and Control provide structure to the project.
Project Deliverables
Project Charter & Business Case
The Lean Six Sigma methodology encourages the use of a project charter and the creation of a business case to set boundaries on the project and to manage stakeholder expectations.
Project Reviews
The Lean Six Sigma methodology involves stakeholders through a set of project reviews. Each type of review has a goal and purpose.
Coaching Stakeholders
Coaching with Questions
Coaching with Feedback
Critical To Quality (CTQ)
Variation
Elements of Waste
Waste can take many forms including high costs, delayed timing, rework, redundant work and idle processes. One of the primary goals of a Lean Six Sigma project is to identify areas of process waste and eliminating or reducing those sources of waste.
Y=F(x)
Process Management
Lean Six Sigma Metrics
Project Selection
One of the decisions that must be made during the Define Phase is the selection of the project and its boundaries. Lean Six Sigma projects are often part of a portfolio of projects that may be selected and approved as a bundle.
Pareto Principle
The Pareto principle is a widely accepted technique for prioritizing effort and activity. The Pareto principle will typically be applied in every phase of a Lean Six Sigma project, including this initial Define phase where it is used to prioritize the areas of focus for the project.
Voice of the Customer
Lean Six Sigma methodology is grounded on the voice of the customer. The Define phase collects and assesses information concerning the customer perspective and uses it to focus the project activities.
Cost of Poor Quality (COPQ)
Process Mapping
In order to improve process performance, the Lean Six Sigma project team must understand the current state of the process. Process Mapping is the technique for describing the process and providing a framework for collecting process data.
Lean Value
Lean Six Sigma projects apply the Lean principle of value-added effort in the definition of the project and when identifying the opportunity for improvement.
Define Stage Deliverables
A Lean Six Sigma Black Belt will often chair the Stage Gate Review meetings for Lean Six Sigma Projects. In those meetings, the Black Belt needs to ensure the work of the phase was done and the tools were used effectively. This lesson reviews the normal deliverables due at the Define Stage Gate review. It also includes hints and tips for identifying problems to be avoided during that phase.
Problem Statement
The problem statement clarifies the goals and activities of the Lean Six Sigma project by specifying the issue to be resolved. It’s an excellent communication tool for the team to use with stakeholders.
Problem Definition Tools
Data Types
There are two types of data: variable and attribute. Both types are useful in measuring process performance by analyzing process problems, but they need to be treated differently.
Measurement Systems
Measurement Errors
X/Y Matrix
The X/Y matrix is a tool that maps the Voice of Customer needs and concerns onto the process steps and inputs. This tool can take on several different formats, but any of them will provide the Lean Six Sigma team with insight as to the contributing factors of customer value.
FMEA Principles
The Failure Mode Effects Analysis (FMEA) tool highlights areas of high product design or process execution risk. This tool provides insight into possible causes for observed failures.
Value Stream Mapping
Value Stream Map Data Box
The Value Stream Map Data Box is the technique used to capture and analyze data at each step of the Value Stream Map.
As-is Metrics
The As-is metrics are the measured current state of the process or problem. It is not the best-case, the worst-case, or the “as-designed” case; it is the current average performance of the process or problem.
Data Collection
The purpose of the Measure phase of a Lean Six Sigma project is to collect complete, accurate and meaningful data. There is a simple data collection approach that can be used by the team to ensure this is accomplished.
Measure Stage Deliverables
A Lean Six Sigma Black Belt will often chair the stage gate review meetings for Lean Six Sigma projects. In those meetings, the Black Belt needs to ensure the work of the phase was done and the tools were used effectively. This lesson reviews the normal deliverables due at the Measure stage gate review. It also includes hints and tips for identifying problems to be avoided during that phase.
Descriptive Statistics
Normal Distribution
The normal distribution charts the type of variability in a process parameter that is being measured when the only cause for variation is natural random physical effects. It’s the desired distribution when improving a process since it delivers a predictable level of process performance.
Basic Graphical Analysis
Graphing of Complex Data
When the process or problem data set has multiple characteristics, there are a set of graphing techniques that can show these effects. Although more complex than the basic techniques, they are easy to use and create a picture of the data set.
Process Stability
Run Chart
Process Capability Principles
Z Scores
Z scores are a method of normalizing data from different data sets for comparison or prediction. Z scores normalize the data using the process standard deviation. The Z transformation table will convert Z scores into percentages.
Central Limit Theorem
The Central Limit Theorem is a principle that is used to transform non-normal raw data into a data set that is normal.
Problem Analysis
Problem analysis is the methodical approach to analyzing a problem and finding the root cause or causes. It normally includes creating and testing an hypothesis or an experiment to determine the cause.
Statistical Analysis
Statistical tests are often used to aid the problem analysis. The statistical analysis of a small sample of data can point to root causes of problems in the full data set.
Visual Analysis
Graphical analysis techniques are particularly good for illustrating significance, similarities or differences, and correlation between parameters within a data set.
Lean Flow Analysis
The Lean process analysis will reveal flow process flow problems. Lean techniques can be used to analyze flow at both a total process (macro) level or at a process step (micro) level.
Lean Quality Analysis
The process analysis of the value stream map will reveal quality issues that are occurring within process steps. These are identified by analyzing step data and process flow data.
Lean Resource Analysis
Analysis of the Lean value stream map and the related data can reveal wasted resources; both people and product or service items that are being processed.
Analyze Stage Deliverables
A Lean Six Sigma Black Belt will often chair the stage gate review meetings for Lean Six Sigma projects. In those meetings, the Black Belt needs to ensure the work of the phase was done and the tools were used effectively. This lesson reviews the normal deliverables due at the Analyze stage gate review. It also includes hints and tips for identifying problems to be avoided during that phase.
Problem Improvement
Problem solving often requires an interim solution while a permanent solution is being developed and validated. When multiple possible solutions are available, the team should recommend a solution approach.
Solving Special Cause & Common Cause Problems
Special cause problems should be resolved first in order to achieve process stability. Then common cause problems are addressed to reduce process variation.
Intro to Design of Experiments
Design of Experiments (DOE) is an experimental technique for identifying the primary factors within a system that determine system performance. DOE is particularly useful in complex systems where there are interactions between factors and relationships are not obvious.
Lean Improvement: Flow
Lean process improvements are designed using a “should be” value stream map that shows the new flow. The data box on this map estimates the impact of the elimination and redesign of process steps and the removal of system constraints.
Lean Improvement: Pull
The benefits of Lean improvements rely on changing the process schedule management approach in addition to process redesign. Pull scheduling and visual management are used to maintain smooth flow in the process.
Solving Problems with Poka Yoke
Many problems can be solved using mistake proofing approaches that are embodied in the five Poka Yoke principles that both detect and prevent errors from occurring.
Solving Problems with Five S Principles
The Five S principles can be used to organize the work place and support and sustain the problem solutions by reducing the likelihood of confusion and rapidly exposing process degradation.
Innovation and Concept Selection
Lean Six Sigma projects normally identify incremental improvements for products and processes. However, sometimes the improvement needed requires innovation beyond the current product and process. This lesson discusses several tools and introduces one of the most popular, the Pugh concept generation matrix, as methods to be used when an innovative solution is required.
Improve Stage Deliverables
A Lean Six Sigma Black Belt will often chair the stage gate review meetings for Lean Six Sigma projects. In those meetings, the Black Belt needs to ensure the work of the phase was done and the tools were used effectively. This lesson reviews the normal deliverables due at the Improve stage gate review. It also includes hints and tips for identifying problems to be avoided during that phase.
Cost – Benefit Analysis
Control Plan
Response Plan
A key element of the control plan is the response plan. It tells the process operators what to do when the process begins to deviate from the parameters laid out in the control plan.
Prevention as Control
Lean Process Control
Lean process control focuses on maintaining the process flow of the Should-Be process. It relies on principles of visual control, empowerment, and continuous improvement.
Statistical Process Control
Statistical process control uses real-time process data to determine whether a process is maintaining the improvements that were implemented. Control charts will indicate special cause and common cause variation, empowering process operators to maintain process quality.
Implementing the Solution
Implementing the technical changes of the solution are often easy, the difficulty is usually the emotional and cultural resistance to change. The implementation should be planned and managed as a project. The project should include the actions taken to change the business systems and structures in addition to the specific problem solution.
Control Stage Deliverables
A Lean Six Sigma Black Belt will often chair the stage gate review meetings for Lean Six Sigma projects. In those meetings, the Black Belt needs to ensure the work of the phase was done and the tools were used effectively. This lesson reviews the normal deliverables due at the Control stage gate review. It also includes hints and tips for identifying problems to be avoided during that phase.
Target Audience
- Graduates exploring placement in the entry-level Lean Six Sigma positions across industries
- Professionals needing upskilling to be future-ready or become more productive in their current roles
- Experienced individuals exploring Lean Six Sigma Advanced Principles – Black Belt.
How do I Access The Program
- Buy the course online
- Save your payment transaction receipt for any future reference
- Our team will share the credentials to enable you access your course online within 2 business days of payment transfer
Bulk Orders
Incase you are looking for bulk user licenses, or customized Learning Paths for various Job Roles, reach out to us with your detailed requirements.
Reviews
There are no reviews yet.